Kaufman's KPAL Series of Robotic Palletizers
Built to meet and exceed expectations and improve your profitability.
Kaufman Engineered Systems is incredibly proud of our KPal series of robotic palletizing solutions! This industry-leading palletizer series will accommodate various product formats, including cases, trays, bundles, and containers.
With over 75 years of experience, Kaufman has built a strong reputation as your premier supplier of reliable and robust equipment. Our proven track record and strong presence in most industries, including food, beverage, paper, health & beauty, personal care, building products, and pharmaceutical segments, speak to our commitment to quality.
The KPal Series of robotic palletizers contains various categories we refer to as groups, so you can further narrow your search by high-level requirements. The Kaufman team can then work with you to further refine those requirements to ensure that we design, build, and install a system tailored to your unique specifications. The end result is a custom automated solution that will increase throughput, lower costs, optimize spacing in your facility, and improve safety.
Consider reviewing the "Cost Considerations" web page via the button below or check out this quick overview of the essential elements of effective palletizing systems for additional information.
Contact one of our experienced account managers to learn how we can streamline your automation. 419-878-9727, info@kes-usa.com
Further Reading: a Essential Elements of Effective Palletizing Systems.
KPal System Videos ---- Cost Considerations ---- Request Quote ---- JOIN OUR MAILING LIST
Technical Aspects of Robotic Palletizing Systems
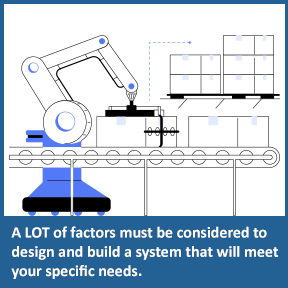
ROBOTIC ARM SPECIFICATIONS
- Payload Capacity: The payload capacity of a robotic palletizing system is one of the most critical technical considerations. It defines the maximum weight the robotic arm can lift and manipulate during the palletizing process. Systems are available with payload capacities ranging from a few kilograms to several hundred kilograms, depending on the nature of the goods.
- Reach and Axis Range: The reach of the robotic arm determines how far it can extend to pick and place products. This, combined with the number of axes (commonly 4-axis or 6-axis), defines the arm's range of motion and ability to handle products from different positions on a conveyor or packaging line.
- Speed and Throughput: The speed of robotic palletizers is measured in cycles per minute or picks per minute (PPM). High-speed robotic palletizers are designed for rapid operations, ideal for industries with high throughput demands. Choosing the appropriate speed ensures seamless integration into production workflows without bottlenecks.
END-OF-ARM TOOLING
- Tooling Design: The end-of-arm tooling (EOAT) is the interface that directly interacts with the products being palletized. EOAT must be designed for the specific shape, size, and weight of the products. There are several types of EOAT, such as suction grippers for lightweight items, vacuum cups for flat surfaces, or mechanical grippers for heavier or irregular-shaped goods.
- Flexibility and Customization: For manufacturers dealing with a wide range of products, EOAT should offer flexibility, allowing for easy changes in tooling to accommodate different product types. Some advanced systems feature automatic tool changers that allow the robot to switch between different tools without manual intervention.
PALLETIZING PATTERNS AND SOFTWARE INTEGRATION
- Palletizing Patterns: A robotic palletizer’s software enables it to create and execute different palletizing patterns. Manufacturers can customize these patterns to optimize pallet space, ensure load stability, and meet packaging specifications. Common patterns include interlocking and column stacking, but systems can be programmed to handle unique or complex patterns as needed.
- User-Friendly Software: Many robotic palletizers come with intuitive software interfaces that allow operators to adjust patterns, speed, and other parameters without deep technical expertise. Manufacturers should look for systems with easy-to-use human-machine interfaces (HMIs) and built-in error detection for smoother operations.
- Integration with Manufacturing Execution Systems (MES): Modern robotic palletizers are designed to integrate seamlessly into larger manufacturing execution systems (MES) or warehouse management systems (WMS). This connectivity enables real-time data tracking, performance monitoring, and predictive maintenance, enhancing operational efficiency.
SAFETY FEATURES AND COMPLIANCE
- Safety Standards: Robotic palletizing systems must comply with global safety standards such as ISO 10218 (Safety Requirements for Industrial Robots) and ANSI/RIA R15.06. Advanced systems include safety features like area scanners, light curtains, and emergency stop mechanisms to prevent accidental collisions or injuries.
- Collaborative Robots (Cobots): For manufacturers looking to integrate robots into human-operated environments, collaborative robots (or cobots) are an excellent choice. These robots are designed with advanced safety features, such as force-limiting technology and proximity sensors, allowing them to work side-by-side with human workers without traditional safety fencing.
CONVEYOR AND MATERIAL HANDLING INTEGRATION
- Automated Conveying Systems: Robotic palletizers are often integrated with conveyor systems that transport products from the production line to the palletizing area. The design of the conveyor system must be compatible with the robotic palletizer to ensure smooth product transfer. Automated conveyors can be equipped with sensors to detect product flow, alignments, and defects before palletizing.
- Automated Guided Vehicles (AGVs) and Autonomous Mobile Robots (AMRs): For fully automated workflows, robotic palletizers can be paired with AGVs or AMRs to transport completed pallets to storage or shipping areas. This integration reduces the need for manual labor and further streamlines logistics within the facility.
PRODUCT STABILITY & LOAD SECURITY
- Load Centering & Stabilization: Ensuring product stability during the palletizing process is essential to avoid load tipping or shifting. Robotic palletizing systems can include centering devices, slip sheet dispensers, and stretch-wrapping equipment to ensure that products are properly aligned and secured on the pallet before transport.
- Dynamic Palletizing: Some advanced robotic palletizing systems feature dynamic palletizing capabilities, allowing the robot to adjust its movements and placement based on real-time feedback from sensors. This ensures load stability, especially when dealing with variable product sizes or weights.
MAINTENANCE & DURABILITY
- Predictive Maintenance: To ensure continuous operation and prevent costly downtime, robotic palletizers are often equipped with sensors that monitor the system's condition. These sensors can predict when components may fail or require maintenance, allowing manufacturers to schedule repairs proactively.
- System Durability: Robotic palletizers designed for industrial use must be built to withstand harsh manufacturing environments. This includes using corrosion-resistant materials, dust-proof enclosures, and components that can handle extreme temperatures or moisture levels.
Videos of KPal Series Robotic Palletizing Systems
FANUC Robotic Full Tier KP1 Palletizing Cell with IR Vision
Full Layer Plastic and Glass Container Depalletizing System
Robotic Bundle Palletizing System
Small Footprint Case Conveying System
K5 Bulk Glass Palletizer System
Robotic Stack and Wrap Palletizing System
High Speed Bag Palletizing System
Each KPal series palletizer is meticulously designed by our experienced engineering team to meet your production needs. Our team works closely with you to optimize the system layout for your plant layout and space constraints. Since each application is unique, our experienced account management team is ready to assist you at every step of the process. Each KPal series palletizer is based on Kaufman’s foundation of robust and reliable architecture, with cutting-edge designs that exceed expectations and improve your bottom line. We look forward to hearing from you soon to discuss your new KPal application.
KPal K5 Group
Full layer & bulk robotic palletizing systems
KPal Group
Robotic palletizing systems
KPal Collaborative Group
Collaborative robotic palletizing systems
Kpal Compact Group
Compact robotic palletizing systems

KPal Stack & Wrap Group
Stack & wrap robotic palletizing systems
KDPal Group
Robotic depalletizing systems
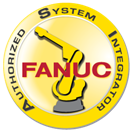
As a level five Authorized Systems Integrator for FANUC Robotics, FANUC's highest level of attainment, Kaufman Engineered Systems applies FANUC robot technology to provide customers with complete end-of-line system solutions.
The solution may be as simple as a dedicated palletizing cell or as complex as a multi-line handling and palletizing system. No matter how big or small, Kaufman Engineered Systems and our preferred partners will address each project and customer with the same integrity and professional response.
Service And Support:
With each KPal system comes Kaufman Engineered Systems service and support. Backed by over 75 years of serving customers, Kaufman is a partner you can rely on to respond quickly and efficiently to service needs. With your KPal palletizer, you will have service options to choose from if you wish to establish quarterly, semi-annual, or annual maintenance support with Kaufman Qualified Technicians.
Kaufman Engineered Systems KPal Series Palletizers. Let us help you become a new member of our family. We look forward to working with you.
KPal System Videos ---- Key Considerations ---- Request Quote ---- JOIN OUR MAILING LIST