Essential Elements of an Effective Robotic Palletizing Systems
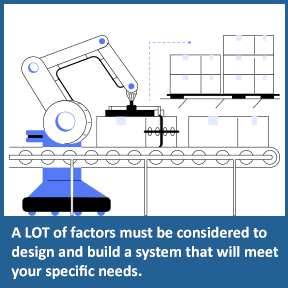
When investing in robotic palletizing systems, several critical factors ensure optimal performance and return on investment:
- Rate: The throughput rate is a pivotal aspect, influencing conveyor speed and the choice of the palletizing robot arm, also known as end-of-arm tooling (EoAT). Understanding your production goals is vital to selecting a system that meets your operational demands.
- Pallet Quality: The uniformity and condition of pallets can significantly affect the system’s efficiency and safety. Ensuring standardized pallet quality is essential to prevent operational hiccups.
- Environment: Environmental conditions, such as temperature and humidity, can impact equipment performance. It is crucial to select materials and designs that withstand specific environmental challenges.
- Case Quality: The dimensions and structural integrity of cases must align with the system’s capabilities. Accurate case specifications ensure seamless operation and minimize costly adjustments.
- Integration: Effective integration of the robotic palletizer with existing systems, including conveyors, stretch wrappers, and warehouse management systems (WMS), is crucial for smooth workflow.
If you're interested in delving deeper into considerations, including qualification details and a cost summary, Read This Cost Analysis Article.
Contact Us ---- Request Quote ---- JOIN OUR MAILING LIST
Typical System Options
Kaufman offers a variety of typical layouts and customizable options to suit diverse operational needs:
- End-of-Arm Tooling: Precision-engineered EoAT options enhance handling capabilities and adaptability across different products.
- Conveyors and Material Handling: Robust conveyor systems streamline product movement, while advanced material handling solutions optimize workflow.
- Safety Equipment: Integrated safety features protect workers and equipment, ensuring a secure operational environment.
- Software & Control Solutions: Kaufman’s advanced control systems and software ensure seamless integration and operation, enhancing efficiency and data management.
- System Layouts: A robotic palletizer cell can have anywhere from one to four product infeed conveyors and from one to four build stations. They can palletize up to four different products on four different build stations, placing any required dunnage (sheets, pallets, frames, etc.) on the load as well.
Why Choose Kaufman Engineered Systems?
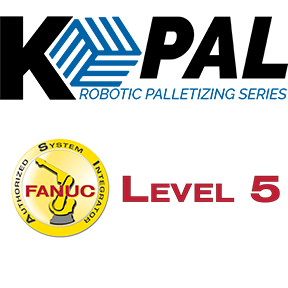
Kaufman Engineered Systems stands out as the premier choice for robotic palletizing solutions, offering a blend of innovation, quality, and customer-focused service:
- KPAL Series: The KPAL series offers versatile solutions for a range of products, including cases, trays, and bundles. Their ability to accommodate various formats ensures flexibility and scalability.
- FANUC Integration: As a Level 5 Authorized Systems Integrator for FANUC Robotics, Kaufman leverages cutting-edge robot technology to deliver complete end-of-line solutions that boost efficiency and reliability.
- In-House Design and Manufacturing: Kaufman’s team of engineers customizes solutions to meet specific requirements, ensuring a tailored approach that enhances operational efficiency.
- Comprehensive Support: With 24-hour service support and a commitment to excellence, Kaufman ensures that systems remain operational with minimal downtime.
Investing in a robotic palletizing system from Kaufman Engineered Systems means choosing excellence and innovation. Their industry-leading solutions, backed by decades of expertise and a dedication to customer satisfaction, make Kaufman the go-to provider for businesses aiming to optimize their palletizing operations. Whether you’re looking to improve line efficiency or reduce labor costs, Kaufman’s robotic systems offer the quality and reliability needed to propel your business forward.
Contact Us ---- Request Quote ---- JOIN OUR MAILING LIST