Cost Summary for a Robotic Palletizer System
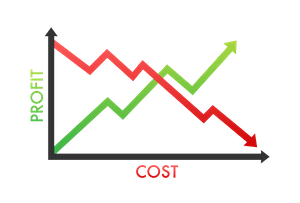
Ideally, the system pays for itself over time and then continues to increase profits for strong ROI.
Six key factors drive the cost of a robotic palletizing cell:
Existing plant layout space/obstacles
End of Arm Tooling
Customer specifications
Control architecture
Safety
Customer case infeed requirements
Costs can range from $175,000 to $550,000, depending on the complexity and requirements of the system.
Request Quote ---- JOIN OUR MAILING LIST ---- Contact Us
Robotic Palletizer Qualification Details
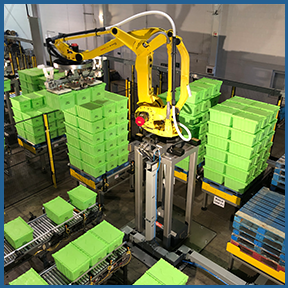
Robotic Tote Palletizer
Robotic tote palletizing system with automated transfer car and rotary arm stretch wrapper.
Overall Project Information
- ROI Analysis: It is crucial to understand how a manufacturer analyzes return on investment (ROI). Different manufacturers have unique ROI calculations, often including factors such as "unavailable labor" and "safety." Evaluating whether a project delivers a favorable ROI compared to other automation opportunities is essential. The initial cost of the system should be offset by the increase in productivity and throughput, lower labor costs, and increased safety so that the system pays for itself over time and then continues to positively impact the bottom line.
- Manufacturing Shift: Operating on two or more shifts (24/7) is typically ideal for comparing the monetary value of robotic automation investment to its cost.
- Timeline: It is important to determine if the OEM/Integrator can deliver the robotic palletizing solution within the customer's time constraints. Matching the lead times with the manufacturer's timeline is critical to offset the initial price and maximize ROI.
- Project Funding: Assess if the project has approved capital funding. Some automation projects are fully funded and sent out for bid, while others require the Robotic OEM/Integrator to assist with concept solutions and budget pricing for capital approval.
Technical Information Required from the Customer
It is imperative for the customer to provide as much detail as possible about their requirements and constraints in order to effectively estimate the price of a system. This section covers some of the information we look for when considering a new project for a customer - it not only helps in determining the cost of a system but achieving the desired results when we design, build, and install the system.
Plant Drawing: The manufacturer must provide details on the installed automation area within the plant. It is vital for the Robotic OEM/Integrator to understand specifics such as:
- I-beam locations
- Ceiling height
- Fork truck aisle/flow
- Truck docks
- Dunnage material flow in and out of the robotic palletizer
- General area for the robotic palletizer
- Existing conveyor system structure
Pallet Pattern: Manufacturers should supply all pallet patterns to be used by the robot.
Case Size and Weight: Detailed information on all case sizes (length x width x depth) and weights, including the product, is needed. This affects the number of products the robot can pick at any given time, determining the robot's size and payload requirements.
Case Type and Rate: Information on all case types associated with each SKU (e.g., RSC, Harness, Tray HSC, Wrap-Around) and the case-per-minute rate is essential. These factors drive the automation solution concepts, affecting the robot's cycle utilization and the number of robots required.
Pallet Size and Type: Manufacturers must provide details on pallet sizes (e.g., 40” x 48”, 56” x 44”) and types (e.g., GMA, Chep, Pico, Plastic). The type of pallet influences the choice of powered conveyor needed to maintain load stability.
Dunnage Requirements: Details on dunnage types and materials, such as top caps, bottom caps, slip sheets, and corner boards, are crucial for the robotic equipment to handle them properly.
Case Orientation: Information on the case orientation at the pick-up point conveyor system (narrow edge leading or wide side leading) is needed to provide the correct infeed conveying solution.
Pick-up/Drop-off Point: Understanding where the scope of conveyor systems begins and ends is essential.
Components of a Robotic Palletizer
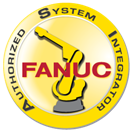
We are a Level 5 Authorized System Integrator for FANUC, the highest level of partnership they have.
Once the project is qualified and information is sent to the OEM/Integrator, it is time to formulate a robotic solution that fits the manufacturer's needs at the best price. Below are common components of a robotic automated palletizing system and their associated costs.
Fanuc Robot: Fanuc is a world leader in automation, offering a comprehensive range of robots for various solutions. The M-410 Series Robots, with payloads from 110KG to 700KG, are commonly used for palletizing. The robot's cost is determined by factors such as load height, product weight, throughput required, and the number of production lines it will serve. Read more.
Control System: The industry standard in the USA is Rockwell Allen-Bradley PLC. Specifications vary, but many manufacturers standardize on Allen-Bradley Compact or Control Logix platforms. Safety PLCs have become common upgrades, offering advantages at increased costs. Read more.
Case Infeed Conveyor: The OEM/Integrator controls the conveyor portion within the robotic palletizing cell. The conveyor system must integrate with the end-of-arm tooling (EOAT) and manage case accumulation for the robot pick/place sequence. Read more. Read more.
End-of-arm tooling (EOAT): Depending on the product to be palletized, various EOAT types (e.g., bag, vacuum, clamp, spatula, and full layer) are used. EOAT characteristics significantly impact the overall system cost. Read more.
Transfer Cars (T-Car): Transfer cars tie multiple robotic palletizing lines to a common stretch wrapper, transporting full loads or dunnage into the robot cell. The distance and throughput rates determine the T-Car requirements and cost. Read more.
Stretch Wrapper: Stretch wrappers secure the load to the pallet. Options include overhead arm, rotary table, and ring wrappers, each suited to different load types. Additional features like load lifters, top hold-downs, and high-speed film carriages may be added. Read more.
Pallet Conveyor: Pallet conveyors, such as chain-driven live roller (CDLR) and chain conveyors, are chosen based on load stability, height, and weight. Accessories like guides, pallet stops, and pushers enhance the system. Read more.
Miscellaneous Conveyor: Based on specific requirements, additional conveyors, such as lift conveyors, vertical lifts, turn tables, chain transfers, drawbridge conveyors, and rotating conveyors, may be needed. Read more.
Dual Load Stacker: This optional equipment stacks two pallet loads, saving floor space and reducing shipping costs. Its justification is based on comparing it to manual stacking by fork truck operators. Read more.
Material Handling: Equipment like pallet dispensers, top sheet dispensers, bins, and halos enhance the robotic palletizing cell's efficiency and stability. Read more.
Safety Equipment: Robot cells can be installed with or without fencing. If without fencing, safety-rated devices like area scanners and light curtains protect personnel. Fencing is more common due to cost considerations. Read more.
Request Quote ---- JOIN OUR MAILING LIST ---- Contact Us