Components of a Robotic Palletizer System
After the robotic palletizer project has been qualified, information sent to OEM/Integrator, and understanding of plant flow it is then time to formulate a robotic solution that best fits the need of manufacture at the best price. Below we will explore common components that make up robotic automated palletizing system and associated cost. Each component is critical to the overall success of the system.
Request Quote ---- JOIN OUR MAILING LIST ---- Contact Us
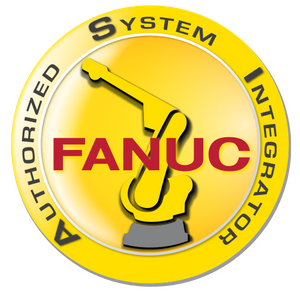
FANUC Integrator
We are a Level 5 Authorized System Integrator for FANUC, the highest level of partnership they have.
FANUC Robots:
Kaufman Engineered Systems is proud to partner with FANUC America, a global leader in automation technologies. This collaboration allows us to provide state-of-the-art robotic solutions that enhance efficiency and productivity for our customers. As a Level V integrator specializing in Pick/Pack/Palletize (Pick/Pack/Pal), Kaufman leverages FANUC's comprehensive range of industrial and collaborative robots to design customized automation systems that meet diverse needs across various industries.
FANUC’s M-410 Series robots, known for their reliability and performance, play a significant role in our palletizing solutions. These robots, with payload capacities ranging from 110KG to 700KG and a work envelope radius between 94.6” to 123.7", can handle multiple production lines simultaneously, optimizing throughput and operational efficiency. Additionally, FANUC’s collaborative robots, with capacities of up to 35kg, offer enhanced safety and flexibility for various palletizing applications.
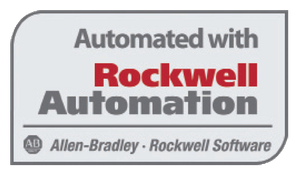
Rockwell Automation
We are a Gold OEM Partner of Rockwell Allen-Bradley PLCs
Control System:
The brains of the system! The industry standard in the USA is Rockwell Allen-Bradley PLCs (Programmable Logic Controllers). Most manufacturers have their own specifications as to the overall control structure of the system to keep common components on the shelf and synergy in staff training. Smaller PLCs, such as AB Micrologix, can be used. However, many manufacturers standardize on the Allen-Bradley Compact or Control Logix platform. More recently, Safety PLCs have become common upgrades. There are many advantages to utilizing a safety PLC, however, at an increased cost. Typical panel size will range from 1-3 door panels with isolated low voltage for arc flash requirements. It is imperative to understand manufacturers' control specifications as the price can be driven significantly up with many upgrades.
Case Infeed Conveyor:
At a minimum, the OEM/Integrator will want to control the portion of the conveyor within the robotic palletizing cell. All cases, whether RSC, trays, or other, will need to be conveyed in, justified, and accumulated for the appropriate robot pick/place sequence. This is where the OEM/integrator's expertise will come into play. The conveyor system will need to integrate with the end-of-arm tooling. (See EOAT). Infeed can be roller conveyor or mat top as two examples. A conveyor can convey into a robot cell a row of products or an entire layer, depending on the overall throughput needed. It is also critical to control back pressure as robots may not be able to pick up a product if there is exceedingly high back pressure. The infeed conveyor works hand in hand with the robot cycle time and sequence of operation. It is paramount that cases are ready to be picked in less time than the robot's overall cycle time, or else the infeed could limit the robot's cycle. Typically, infeed case length at a min. is 10’-15’. However, the end user may require in RFQ the system integrator to include hundreds of feet of conveyor upstream, thus driving the cost of the system up. If so, OEM/Integrator will require a thorough understanding of conveyor systems such as merges, sort, diverts, brake/meter belts, and speed/gapping to achieve desired results. Lastly, palletizing robot vertical reach allows for case conveyors to enter the robot cells at a low elevation off the floor or elevated elevation suspended from the ceiling, all of which drive cost.

End-of-Arm Tooling (EOAT):
All components within a robot palletizing cell can be perfect; however, if the end of arm tooling can not pick or place the product, then the overall solution is a failure. There are many types of EOATs depending on the product to be palletized. Below are a few examples:
- Bag EOAT - 20lb-50lb of bags.
- Vacuum EOAT – Typically used for RSC cases.
- Clamp EOAT – For products that cannot be vacuumed.
- Spatula EOAT – For open top cases that cannot by clamped.
- Full Layer EOAT – For palletizing or depalletizing a full layer of product at a time
End-of-arm tools can either be hard-wired back to the robot I/O or use E-net for communication. With complex tools, it is easier to use block I/O on the end of the robot and run Cat-5E back to the robot controller. This eliminates considerable wiring. Expert OEM/Integrators will evaluate customer products in R&D. Although a product may be able to be picked by vacuum, for example, the product may not be able to stay on EOAT depending on the speed and inertia that the robot needs to run to meet the customers' cycle throughput. As a result, at a minimum, the tool may need accessories to help control the case during moving, and at an extreme, a second robot may be required to run at slower speeds to meet the rate. The EOAT carry characteristics play a key role in the overall cost of the system.
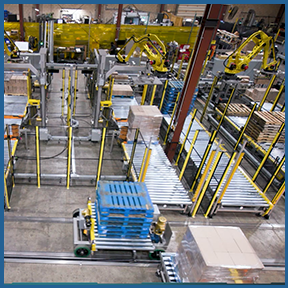
Transfer Cars (T-Cars):
Transfer cars are used to tie multiple robotic palletizing lines together to a common stretch wrapper. They can pick up full loads and/or deliver dunnage into the robot cell. Distance transfer car needs to travel in relationship to customer throughput rates dictate T-Car required. Options are from a slow-speed single car up to a high-speed, 300 FPM quad car laser positioned with an overhead electrical power rail system and embedded floor track. Transfer cars can be outfitted with hold-downs for unstable products. Another consideration that drives price is whether the T-car is within a fenced area or not. If not, additional safety costs will be required. These units travel in a linear motion and are invaluable to the overall solution of robotic palletizing cells.
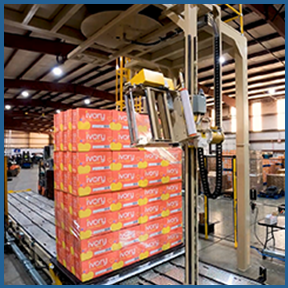
Stretch Wrapper:
The stretch wrapper is an instrumental part of the robotic palletizing cell and is the most common way today to secure the load to the pallets. Typical flavors of stretch wrappers include overhead arm, rotary table, and ring wrapper. Each model has its own advantages that are mostly driven by load type. The overhead arm rotates an arm around the load while keeping the load stationary. The rotary table keeps the film head stationary while rotating the load. The ring wrapper rotates about the load while the load is conveyed through the center of the ring. Think of 12’ house siding conveying through the center of the ring wrapper while being stretch-wrapped. If a customer has a short, stable load with a tight footprint, then a rotary table will be the best option. If there is a tall, unstable load, then an overhead arm may be the best option. Stretch wrappers have available plugin options depending on customer package needs. Load lifters can be placed within the pallet conveyors to lift the load, thus ensuring complete wrap of the pallet or load itself. Top hold downs can be implemented for additional stability dependent on load type. Gravity or powered transition rollers can be added to help power a load into the stretch wrapper. High-speed film carriages can be added to help apply the correct amount of film to high-speed stretch wrappers. Plows can be used to fold up/down top and bottom caps to complete customer packages. Robotic corner boards can be added to the stretch wrap sequence of operation depending on the customer's overall package needs. There are software options as well, such as (CAM – corner anticipation mode) Depending on customer load, it may not be enough to rely on the payout of film around the corner of the load via hardware components. As an example, if a customer has a short load of toilet paper, the tension in the film at the corner of the load may pull in and round out the toilet paper, which would be an inherent problem for the consumer. CAM - corner anticipation mode, would pay out the extra film at the corner of the load via software by anticipating the corner, thus ensuring toilet paper does not get rounded.
Pallet Conveyor:
There are two main pallet conveyor systems within a robot palletizing cell: chain-driven live roller (CDLR) and chain conveyor. Each conveyor has its own unique characteristics depending on pallet and load type. How stable is the product when being conveyed? What is load height and weight? Is the load conveyed on a pallet or bottom sheet? For example, if the manufacturer has a glass bulk load 110” tall over 3000 pounds, a 3-strand chain conveyor would be chosen to support the load and provide a smooth and stable transition while conveying. If the manufacturer has a short stable load with a GMA pallet wide side leading, then CDLR would be the chosen conveyor. Pallet conveyors can be outfitted with accessories such as guides, pallet stops, and pallet pushers to justify load as examples. All these different scenarios are taken into consideration when developing a robotic palletizing solution. Not all conveyors are built the same, which is why it is important for customers to have a thorough understanding of manufacturing practices by Integrator/OEM. Items to consider are bearing used, number of legs per conveyor, formed or welded, zinc-plated roller, etc. If the manufacturer is picking up a 3000-pound load via fork truck every 60 seconds (60LPH), the end user will want a robustly built conveyor.
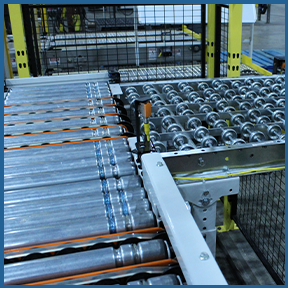
Miscellaneous Conveyors:
In addition to standard pallet conveyors, there are many types of miscellaneous conveyors that may be needed in a robotic palletizing cell. Lift conveyors may be needed for small elevation changes. Vertical lifts such as Qimarox or Ryson may be utilized to elevate or descend cases into robotic palletizing cells. A high/low pallet conveyor can be used to pick up a full pallet load on the upper deck while transporting empty pallets on the lower deck. Turn tables and chain transfer would be used for pallet orientation changes to present and convey pallets in proper form. As an example, fork truck operators may need to perform a side load pick-up on a GMA pallet based on plant flow. Therefore, the OEM/Integrator will need to present the pallet to the fork truck operator with a 48” dimension across the conveyor, leaving open pockets on the side load. This would dictate the use of a chain transfer or turntable. Special robot pick conveyors may be required to specifically integrate with robot end of arm tooling. Drawbridge conveyors can be utilized to access robot cells when required for maintenance purposes. Rotating conveyors are used to flip a product right side up or onto its side for robot pick. In summary, there are many misc. type conveyors depending on customer needs that affect the overall design and cost of a robotic palletizing system.
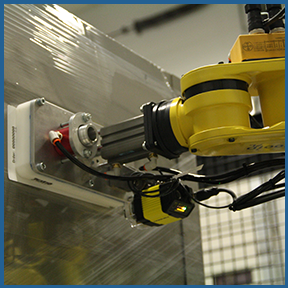
Robotic Labeler:
Manufacturers will apply a label to full pallet loads after the stretch wrap process. A robotic labeler is an alternative option to a mechanical unit. The cost of a robot can be justified typically when applying more than one label to a load, especially at different heights if, for example, the load is double stacked. Additionally, the end-of-arm tooling can be outfitted with a scanner wired back to the PLC. This allows a check to confirm a label has been placed. Also, the scanner can scan the actual bar code and compare it to a look-up table in the PLC confirming the product code. The obvious advantage of robotic technology vs mechanical is the flexibility that the robot offers. When product packages change, affecting the height of the load and label position, it’s simple to reprogram the robot.
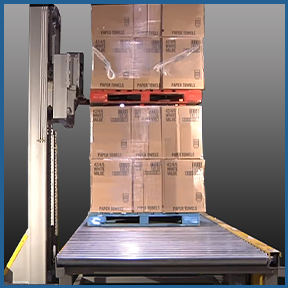
Dual Load Stacker:
A dual-load stacker is an optional piece of equipment that can be added to any robotic palletizing cell. The purpose of a stacker is to stack two pallet loads of product on top of one another. Typically, short loads will be double or triple-stacked for storage and/or shipped directly to consumers. This allows manufacturers to save valuable floor space while storing and shipping costs. A dual load stacker is usually easily justified when compared to a fork truck operator manually stacking loads. Many manufacturers also include wear and tear of fork trucks in the ROI calculation.
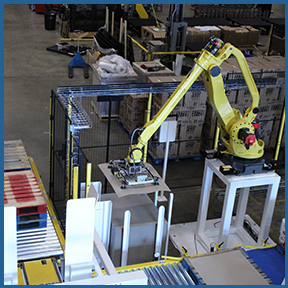
Material Handling:
There are many types of material handling equipment that can be added to a robotic palletizing cell. A few common options are a pallet dispenser, a top sheet dispenser, bins, and a halo for robot-build stability. Usually, pallets within a robot cell are either dispensed in via a pallet dispenser or a stack of pallets are delivered by a fork truck. If dispensed in, then either robot EOAT can pick/place the pallets, or the pallets will be conveyed directly into the pallet build location. If the pallet stack is conveyed in, then the robot will be equipped with pallet tynes to pick/place the pallets directly onto the build location. Bins will be used to hold dunnage material that is used to make up the unit load. Examples of dunnage could be corner boards, tier sheets, bottom sheets, and top caps. It is not uncommon to have multiple bins within a single robotic palletizing cell. A sheet dispenser can be an electrical/mechanical device that dispenses sheets into a robot cell or presents a single sheet to the robot for picking/placing. Dispensers may be used to reduce robot cycle utilization. Halos are used around the circumference of the build location and work in unison with the robot palletizer to ensure the entire layer is held together while robotic palletizing is in operation. An example where a halo would be utilized would be when palletizing full-layer, light plastic bottles. The halo would ensure no product would fall to the floor while the robot is placing the tier sheet.
Safety Equipment:
Robot cells can be installed with or without fencing. If without fencing, then numerous safety rated devices will be used to protect people from equipment. This is typically performed with area scanners and light curtains. More commonly, due to expense, robot cells are installed with physical fencing. Fanuc Robotics uses a software technology called “Dual Check Safety.” DCS utilizes redundant safety systems, which allow OEM/Integrator to reduce floor space requirements. This software package creates boundaries to keep the robot's work enveloped within. Collaborative robots can be installed without fencing, only if run in collaborative mode (speed). Typically, due to speed and robot operating in the head/neck region, additional safety devices are required.
Experience Unmatched Efficiency with Robotic Solutions Designed, Built, and Installed by Kaufman Engineered Systems
As a leader in automation solutions, Kaufman Engineered Systems specializes in providing top-tier robotic palletizer system components that transform your production process. Our comprehensive range of products and services, coupled with our unwavering commitment to quality and innovation, sets us apart as the go-to partner for all your automation needs.
Comprehensive Product Offerings: Our robotic palletizer systems encompass an array of components designed to work seamlessly together. From advanced robotic arms and grippers to precision conveyor systems and customized end-of-arm tools, we provide everything you need to optimize your palletizing operations. Each component is engineered to deliver exceptional performance, reliability, and durability, ensuring your system operates at peak efficiency.
Unrivaled Quality and Workmanship: At Kaufman, quality is the cornerstone of everything we do. Our systems are built using the highest-grade materials and cutting-edge technology, adhering to rigorous industry standards. Our meticulous attention to detail ensures that each component is crafted to perfection, providing long-lasting value and superior functionality.
Decades of Experience and Expertise: With over [insert number] years of experience in the industry, Kaufman Engineered Systems has honed its expertise in designing and implementing automation solutions across various sectors. Our team of seasoned professionals brings a wealth of knowledge and skill to every project, ensuring that we deliver tailored solutions that meet the unique demands of your business.
Benefits of Choosing Kaufman: Partnering with Kaufman means gaining access to a host of benefits:
- Increased Productivity: Our robotic palletizer systems streamline your operations, boosting throughput and minimizing downtime.
- Enhanced Precision: Advanced robotics ensure accurate and consistent palletizing, reducing errors and improving product quality.
- Scalability: Our systems are designed to grow with your business, allowing for easy upgrades and expansions.
- Cost Efficiency: By automating labor-intensive tasks, our solutions help reduce operational costs and improve overall profitability.
Innovative Solutions for Modern Challenges: Kaufman Engineered Systems is dedicated to staying ahead of the curve. We continuously invest in research and development to bring you innovative solutions that address modern production challenges. Our commitment to innovation means that you can trust us to provide cutting-edge technology that keeps your operations competitive and efficient.
Partner with Kaufman Engineered Systems
When you choose Kaufman Engineered Systems, you're choosing a partner committed to excellence, innovation, and customer satisfaction. Let us help you revolutionize your palletizing & packaging operations with our state-of-the-art robotic systems. Contact us today at 419-878-9727 or click one of the buttons below to learn more about our offerings and request a personalized consultation. Experience the Kaufman difference and take your automation to the next level.
Request Quote ---- JOIN OUR MAILING LIST ---- Contact Us ---- Back to Cost Overview