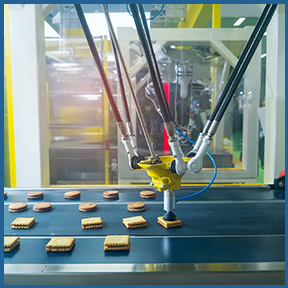
Food Packaging Automation Systems: Key Technical Considerations
In the fast-paced world of food production, where efficiency, hygiene, and scalability are paramount, food packaging automation systems have become an indispensable tool for manufacturers. Companies like Kaufman Engineered Systems specialize in designing and implementing robotic systems tailored to meet the unique needs of food packaging processes. Below, we delve into the critical technical considerations that guide the creation of these advanced systems.
Today is the day to maximize the efficiency of your material handling needs. Contact our award-winning account managers for a free consultation. Call 419-878-9727 or email us at info@KES-USA.com.
Product Versatility & Flexibility
Modern food packaging automation must handle a wide variety of products, shapes, and packaging styles. To meet these demands, robotic systems are designed with flexibility in mind. This includes:
- End-of-Arm Tooling (EOAT): Custom EOATs allow robots to handle diverse packaging types such as bags, pouches, cartons, or shrink-wrapped items without compromising speed or accuracy.
- Multi-Product Handling: Systems should seamlessly switch between different SKUs or product types with minimal downtime, leveraging vision systems and automated changeover technologies.
Hygienic Design Standards
Food safety regulations necessitate meticulous attention to hygiene in packaging automation. Key considerations include:
- Sanitary Design: Utilizing stainless steel or other non-corrosive materials ensures the system withstands frequent washdowns and complies with FDA and USDA standards.
- Minimized Contamination Risk: Enclosed designs and clean-in-place (CIP) capabilities help reduce contamination risks, particularly in environments handling raw or ready-to-eat foods.
Integration with Upstream & Downstream Processes
Seamless integration with existing production lines is essential for a cohesive operation. Kaufman Engineered Systems achieves this through:
- Advanced Programmable Logic Controllers (PLCs): PLCs allow for precise coordination with upstream processes like filling and sealing, and downstream activities like labeling and palletizing.
- Scalable Interfaces: Modular designs enable future expansion, accommodating additional equipment or functionality as production needs evolve.
Speed & Throughput Optimization
To meet market demands and maintain competitive production schedules, systems must operate at high speeds without sacrificing accuracy. Technical solutions include:
- High-Speed Robotics: Delta and SCARA robots, known for their speed and precision, are commonly employed in primary and secondary food packaging.
- Advanced Sensors and Vision Systems: High-resolution cameras and AI-powered algorithms detect and correct misaligned or defective products in real-time.
Durability & Reliability
Food packaging environments are often harsh, involving temperature fluctuations, high humidity, or abrasive materials. Reliable systems are:
- Built to Last: Components like gearboxes, motors, and conveyor systems are engineered to endure continuous operation.
- Predictive Maintenance Integration: Sensors monitor wear and tear, alerting operators to potential failures before they disrupt production.
Energy Efficiency & Sustainability
Sustainability is a growing priority in the food industry. Automation systems contribute through:
- Energy-Efficient Motors: Variable frequency drives (VFDs) reduce energy consumption without compromising performance.
- Material Optimization: Robots precisely dispense packaging materials, minimizing waste and reducing costs.
Safety Features & Compliance
Worker safety remains a top priority. An effective food packaging automation system includes:
- Collaborative Robots (Cobots): Cobots work safely alongside human operators, reducing the need for extensive safety barriers.
- Emergency Stop Systems: Intuitive controls and failsafes ensure the system shuts down immediately in case of a malfunction.
- Regulatory Compliance: Systems adhere to OSHA and ANSI standards, providing peace of mind for manufacturers.
Data Integration & Industry 4.0
Modern food packaging systems embrace the principles of Industry 4.0 for data-driven decision-making. Considerations include:
- IoT Connectivity: Sensors and devices transmit real-time data, enabling predictive analytics and improving operational efficiency.
- Centralized Monitoring: SCADA systems provide operators with a comprehensive view of system performance, making troubleshooting and optimization straightforward.
Why Choose Kaufman Engineered Systems?
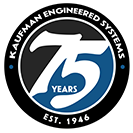
Kaufman Engineered Systems exemplifies innovation and reliability in food packaging automation. By combining decades of engineering expertise with cutting-edge robotics, Kaufman delivers tailored solutions that enhance productivity, reduce operational costs, and ensure compliance with stringent food industry standards. Their turnkey approach—from initial consultation to installation and ongoing support—ensures every system is optimized for the specific needs of each customer.
Request Quote ---- Contact Us ---- JOIN OUR MAILING LIST