Custom Robotics Case Packer for Delicate Filters in High-Speed Operation
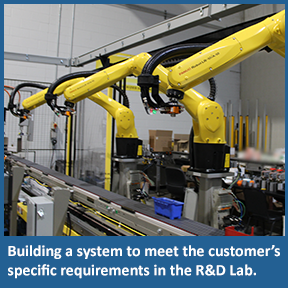
PROBLEM:
A filter manufacturer needed to automate their case packing process for large volumes of delicate filters. These filters are lightweight, highly deformable, and come in various shapes (flat-bottom, cone-shaped) and filter counts. Standard case packers were either too rough, causing damage or deformation to the filters, or could not handle the precise placement required to fit them efficiently into cases. Manual packing was too slow and error-prone, leading to productivity bottlenecks.
Request Quote ---- Contact Us ---- JOIN OUR MAILING LIST
CUSTOM SOLUTION:
The solution utilized 3 in-line FANUC LR-10iA/10 robots to create a case packing solution designed specifically for handling lightweight, fragile filters at high speeds while maintaining precision and product integrity.
- Line Layout - Reverse continuous flow, line tracking application with FANUC software to help balance input load between the 3 robots. Depending upon set-up, each robot would pick between 1-3 filters per pick.
- Testing/R&D - The initial concept was developed with FANUC Roboguide software. EOAT was developed and tested in Kaufman Engineered Systems R&D lab
- Custom EOAT - Filters had a plastic bag around them, presenting an additional layer of complexity. Out of bagging sequence, air was left inside bag. To properly case pack and for all filters to fit within the case, the air needed to be depleted. Developed a custom EOAT that not only picked all the various sizes of filters but also integrated into tooling a mechanism that would push air out of the bag.
- Precise Guided Positioning System - The scope of a project originally started with an integrated vision. A single camera was set up at the trigger point and tracked through to robots. Although the customer was not opposed to a vision solution, they pushed for a simpler setup that maintenance could easily adapt to without the need for outside help. A small servo-driven device was installed at the trigger point that served two purposes: 1. Position the filters exactly on the conveyor belt each time, and 2. Gap filters correctly down the conveyor line. This simplified the positioning system at a reduced cost and ensured that the robot adjusted to the position of each filter stack precisely, placing them neatly into cases without damaging or compressing the filters.
- Case Feeding Mechanism - A case feeding system was integrated to accommodate the different filter packaging formats. The system adjusts as required based on the size and shape of the filter stacks, preventing movement or misalignment inside the case during the packing process. A side belt gripper was used for this specific application.
- Flexible Case Loading - The robotic system can manage multiple case sizes and configurations, adjusting as required for different SKUs. This flexibility is key for manufacturers who package several types of filters for different markets (e.g., commercial vs. home use) without having to retool the system.
- High-Speed Stacking and Packing - To meet high-volume production needs, the robotic system can stack and pack up to 95 filters per minute without compromising precision or product integrity. This is accomplished through a combination of optimized robotic motion and intelligent spacing of the filters inside the case to prevent crushing.
RESULTS:
This robotic case packing solution increased the manufacturer’s throughput by 50% while reducing product damage and waste by 70%. Labor costs for manual packing were cut significantly, and the system’s adaptability allowed for rapid packaging of different filter types without downtime for reconfiguration.
WHY IT'S UNIQUE:
This custom robotic case packer addresses the challenges of handling lightweight, deformable products like filters that traditional case packers cannot manage without causing damage. By combining soft-touch vacuum grippers, precision-guided positioning, and Fanuc robots, the system provides the precision and care needed for delicate product handling at scale. This level of customization makes it a standout solution compared to standard case packers, which are better suited for rigid, uniform products.
Request Quote ---- Contact Us ---- JOIN OUR MAILING LIST