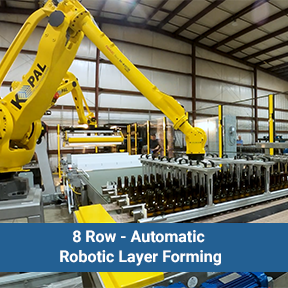
Automated System for Bulk Palletizing Glass Bottles
Kaufman Engineered Systems designed, built, and installed a comprehensive system for bulk palletizing glass bottles for a customer specializing in producing and distributing bottles for their customers. The system was designed to meet the customer's specific requirements for cycle times and stability of completed loads for maximum productivity. The system utilizes two FANUC M-410i B/140H robots and one FANUC M-410i C/500H robot, along with a system Kaufman built to securely strap down completed loads.
Contact Us Today for information on what Kaufman Engineered Systems can do for you!
THE CHALLENGE:
The customer needed an automated system to palletize glass bottles in bulk quickly and securely while utilizing a small footprint within the facility's existing floorspace and without impacting the yearly planned furnace outage. The furnace that makes the bottles turns out 800 bottles per minute. The palletizing system must keep up with this nominal rate with the ability to increase to a surge rate of 900 bottles per minute for short durations.
Key challenges:
- Design & build a system with a small footprint to reuse existing plant space
- Incorporate pallet strapping at the palletizer to reduce the conveying distance required for unstrapped and unwrapped loads
- Demolition of existing obsolete palletizer and successful installation of the new system must be completed during the plant's short yearly allowance for furnace outage
- Program a dynamic system to handle swings in bottle rate along with automatic delivery of pallets, sheets, and top frames (dunnage)
THE SOLUTION:
Kaufman Engineered Systems (KES) designed this KPal K5 Full Layer Bulk Glass Palletizing System to palletize bottles in bulk utilizing the customer's pallets, sheets, and top frames (dunnage). In our custom design, KES used two FANUC M-410i B/140H robots and one FANUC M-410i C/500H robot. Each robot utilized a KES designed & built end-of-arm tool (EOAT), including:
- FANUC M-410i C/500H with a KES patented K5 full layer drawer tool
This patented tooling allows our systems to pick full layers from glass bottles to open trays, cases, plastic, and bundles, making it one of the most versatile tools in the industry
- FANUC M-410i B/140H with a KES-designed & built dunnage tool to pick pallets, sheets, and top frames
- FANUC M-410i B/140H with a KES-designed & built sweep tool to receive 8 rows of bottles and form them into a 44"x56" tier
The system palletizes 440 bottles per tier and builds 10 layers per pallet for a total of 4,400 bottles on finished loads. The system effectively delivered the required cycle times, running 800 bottles per minute nominal and 900 bottles per minute surge rates. With the customer's old palletizing system, each palletized load, weighing nearly 3,000 lbs and standing 90" tall, had to convey over multiple pallet conveyors for several minutes before being secured with strapping. KES designed the new system to incorporate a secure strapping system into the palletizing cell to ensure the stability of the finished loads immediately after palletizing.
We integrated the customer's existing dunnage delivery system with our own Dynamic Dunnage system to ensure pallets, sheets, and top frames would always be accessible to the FANUC robot outfitted with the dunnage tool. The Dynamic Dunnage system locks in one position for pallets, one for sheets, and one for top frames while monitoring the level for each, allowing the KES program to call for the next piece of dunnage needed automatically. This ensures the palletizer has a spare stack of dunnage as soon as the last pallet, sheet, or top frame is used, preventing unnecessary stops in the production line. KES Dynamic Dunnage also incorporates the top frame and sheet pallets into the dunnage pallet stack to be used as needed so that operators are not required to remove heavy pallets from the palletizer while reducing the number of pallets that need to be delivered to the palletizer.
KES custom programming also built a bottle monitoring system to continuously oversee the accumulation of bottles needing palletization and adjust robot speeds accordingly to ensure the palletizer is constantly running at an optimal rate. This prevents unnecessary wear and tear on critical components while safeguarding against bottles backing up into upstream processes.
Finally, Kaufman designed, built, and tested the system thoroughly in-house before sign-off so that we could complete a turnkey install and start-up of the system on-site during a very short furnace outage lasting approximately a week.
Find out how Kaufman Engineered Systems can increase your productivity, lower your labor costs, and improve safety at your facility:
Contact Us ---- JOIN OUR MAILING LIST ---- Request Quote